Exclusive Discount
We are pleased to offer a 30% discount on all items valued at more than $1,000. This initiative is designed to make it easier for our customers to acquire these exquisite, handcrafted statues. Our goal is to ensure that the beauty and craftsmanship of these pieces remain accessible while maintaining the highest standards of quality and authenticity.
This discount reflects our commitment to supporting collectors, practitioners, and art enthusiasts in their pursuit of meaningful, high-quality statues. Should you have any questions or require assistance, please feel free to reach out.
Dipankara one of the Buddhas of the past, said to have lived on Earth one hundred thousand years.
Theoretically, the number of Buddhas having existed is enormous and they are often collectively known under the name of "Thousand Buddhas". Each was responsible for a life cycle. According to some Buddhist traditions, Dipankara (also Dipamkara) was a Buddha who reached enlightenment eons prior to Shakyamuni, the historical Buddha. Generally, Buddhists believe that there has been a succession of many Buddhas in the distant past and that many more will appear in the future; Dipankara, then, would be one of numerous previous Buddhas, while Shakyamuni was the most recent, and Maitreya will be the next Buddha in the future.
Chinese Buddhism tends to honor Dipankara as one of many Buddhas of the past[citation needed], which forms with Shakyamuni (Buddha of the present) and Maitreya (Buddha of the future), the Buddhas of Three Times.
Mahayana text named the Sangatha Sutra.
Dipankara is generally represented as a sitting Buddha, but his depictions as a standing Buddha are common in China, Thailand, and Nepal; with the right hand he generally forms a protection mudra (abhaya mudra), and often he forms it with both hands.
He is rarely depicted alone; one of the Buddhas of Bamyan, destroyed by the Taliban government in Afghanistan in 2001, was said to portray Dipankara. Statues of Dipankara can also be found in the Longmen and Yungang Grottoes in China.
He is generally depicted with two Bodhisattvas, Manjushri and Vajrapani (common in Java) or Avalokiteswara and Vajrapani (common in Sri Lanka); or with the Buddhas who come after him, Gautama and Maitreya.
Prediction
One story recounts a meeting between Dipankara Buddha and Shakyamuni, many lifetimes before Shakyamuni's eventual enlightenment. When Dipankara told Shakyamuni he would one day become a Buddha, Shakyamuni replied, "I am to become a Buddha, awakened to enlightenment; may you tread with your feet on my hair - on my birth, old age, and death." Dipankara Buddha then said, "Freed from human existence, you will become an effective teacher, for the sake of the world. Born among the Shakyas, as the epitome of the Triple World, the Lamp of all Beings, you will be known as Gauthama. You will be the son of King Suddhodana and Queen Maya. Shariputta and Moggallana will be your chief disciples. Your caretaker will name as Ananda"
In 45 years life of the Buddha, said almost 554 past life stories, Jaathaka Katha in Sinhalese of himself. Gauthama Bodisatta, a person starts the journey to become a Buddha filling 10 Paramita, was born in the time of Dipankara Buddha, and was rich and gave away all his wealth to become a Monk. It is said that Gauthama Bodisatta received his first Niyatha Vivarana, definite foresighting by a Buddha, from Dipankara Buddha. This encounter, among many other predictions of Shakyamuni Buddha's future enlightenment, can be found in a
Bronze finishing
Buddha
Gautama Buddha, popularly known as the Buddha, He is regarded as the founder of the world religion of Buddhism, and revered by most Buddhist schools as a savior, the Enlightened One who rediscovered an ancient path to release clinging and craving and escape the cycle of birth and rebirth. He taught for around 45 years and built a large following, both monastic and lay. His teaching is based on his insight into the arising of duḥkha and the ending of duhkha the state called Nirvana
Read More
The Buddha was born into an aristocratic family in the Shakya clan but eventually renounced lay life. According to Buddhist tradition, after several years of mendicancy, meditation, and asceticism, he awakened to understand the mechanism which keeps people trapped in the cycle of rebirth. The Buddha then traveled throughout the Ganges plain teaching and building a religious community. The Buddha taught a middle way between sensual indulgence and the severe asceticism found in the Indian śramaṇa movement. He taught a training of the mind that included ethical training, self-restraint, and meditative practices such as jhana and mindfulness. The Buddha also critiqued the practices of Brahmin priests, such as animal sacrifice and the caste system.
A couple of centuries after his death he came to be known by the title Buddha, which means "Awakened One" or "Enlightened One". Gautama's teachings were compiled by the Buddhist community in the Vinaya, his codes for monastic practice, and the Suttas, texts based on his discourses. These were passed down in Middle-Indo Aryan dialects through an oral tradition. Later generations composed additional texts, such as systematic treatises known as Abhidharma, biographies of the Buddha, collections of stories about the Buddha's past lives known as Jataka tales, and additional discourses, i.e. the Mahayana sutras.
Bronze Finishing
This Buddha product features a stunning Bronze patina finish. Our store takes pride in offering this exclusive patina, which involves a meticulous process utilizing organic materials such as butter and vegetable color. The aim is to recreate the appearance of an aged bronze statue, evoking a sense of timeless elegance.
The art of giving the bronze color to red copper is truly exceptional and is practiced by skilled craftsmen. With each piece, you not only acquire a beautifully finished Buddha product but also pay homage to the artisans who are dedicated to preserving this rare and fading art form. The result is a unique and captivating aesthetic that adds a touch of sophistication and nostalgia to any setting.
Why use bronze Color?Bronze color refers to the distinctive hue that is characteristic of bronze metal. It is a rich, warm tone that falls somewhere between brown and copper. Bronze has been used for centuries in the creation of statues, sculptures, and various decorative items due to its unique aesthetic appeal.
While the production of bronze statues can be complex and challenging, particularly in the Nepali statue-making industry, the bronze color can still be achieved through alternative methods such as the Bronze finishing process. In Nepal, sand casting is commonly used for creating bronze statues, but the resulting quality may not always meet desired standards. The Lost Wax system, on the other hand, yields better quality but can be prone to damage during the intricate carving process, leading to a decline in its practice.
Despite the challenges faced in creating bronze statues, the Bronze finishing process offers a way for individuals who appreciate the appearance of bronze to still experience its allure. By applying this finishing technique to other materials, such as Buddha, individuals can enjoy the look and feel of a bronze statue while preserving the essence of this revered art form.
Example of Bronze finishing
Read More
Lost-Wax System
This Buddha is made by the process of the Lost-Wax system. The lost-wax process, also known as investment casting, is a time-honored technique used to create metal sculptures. It involves several steps that have been practiced for thousands of years. Skilled artisans begin by sculpting a detailed wax model, capturing every intricate detail of the desired sculpture. The wax model is then coated with a ceramic shell, formed by multiple layers of ceramic material. Once the shell has cured, the wax is melted and drained out, leaving behind a cavity. Molten metal is poured into the cavity, creating a precise replica of the original wax model. After the metal has cooled and solidified, the ceramic shell is carefully removed, revealing the final metal sculpture.
Process of loss wax systemThe lost-wax process offers exceptional quality control and customization, making it a preferred choice for artists seeking intricate and personalized metal artwork. Despite the availability of newer methods, the traditional lost-wax technique continues to be valued for its historical significance and the craftsmanship it embodies.
The method of metal casting in which molten metal is poured into a mold that has been created by means of a wax model. Once the mold is made, the wax model is melted and drained away. Bronze statues come to life differently than marble statues. Instead of carving a block or marble, the bronze artist uses the lost-wax technique to make a series of molds and then pours melted bronze into the final mold to create the sculpture. This method has been around since 4500 BCE.
There are a few important steps in the lost wax casting process:
Step 1: Sculpting ( It all starts in the studio with an idea, Then figuring out how to realize the vision in clay.)
Step 2: Mold Making.
Step 3: Wax Pouring.
Step 5: Wax Spring.
Step 6: Shell Dipping.
Step 7: Bronze Pouring.
Interestingly enough Loss wax process is also called Investment casting because after layers have been formed and dried, the wax is melted out of the ceramic tree by using steam (120°C) in an autoclave. This is why it is called "lost wax casting". The majority of the molten wax can then be regenerated and reusable.
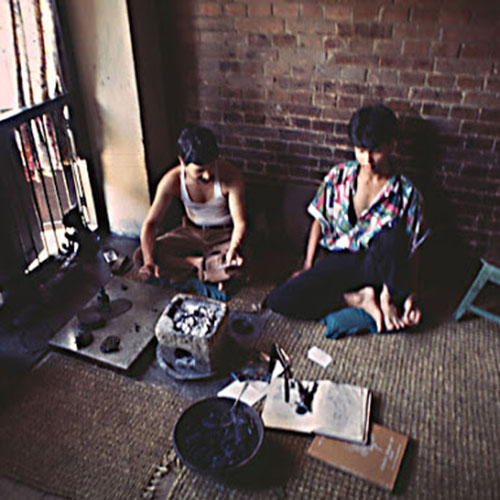 Before Making statue :At work room making the wax models. | 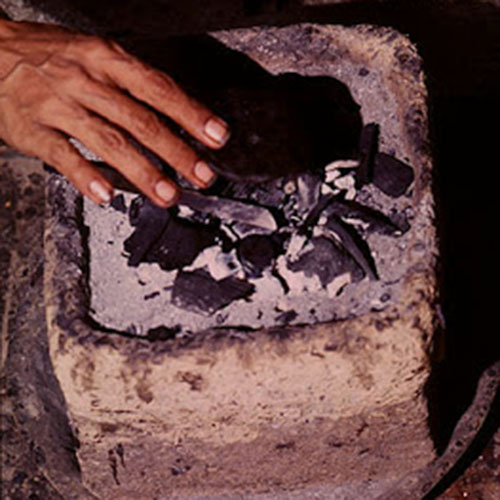 Softening a piece of wax over a brazier. | 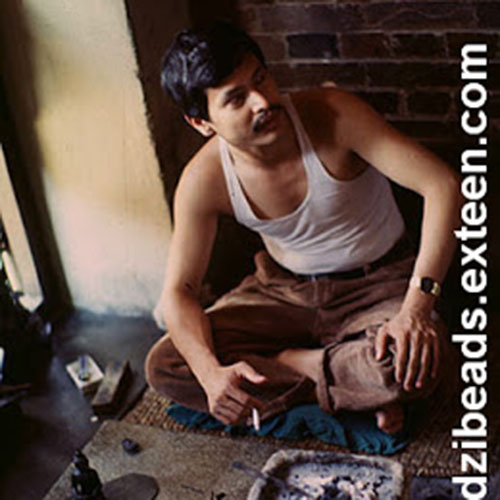 Relaxing after softening the wax The working environment with works in progress. |
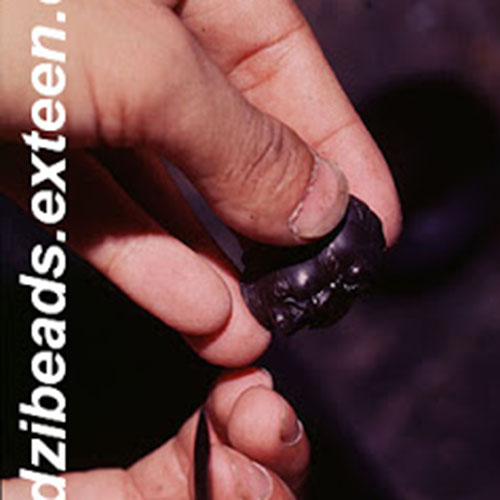 Working the face of an Ekajata wax model. | 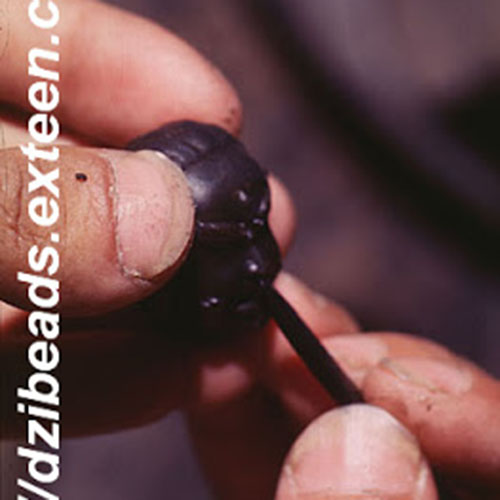 Working the face of wax model.Using a modeling tool to form the face of Ekajata. | 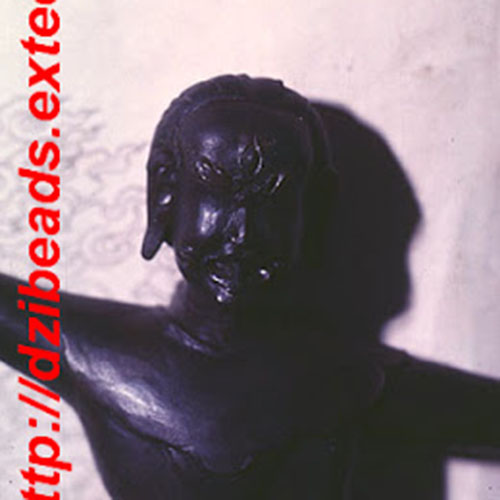 Deatail of wax model |
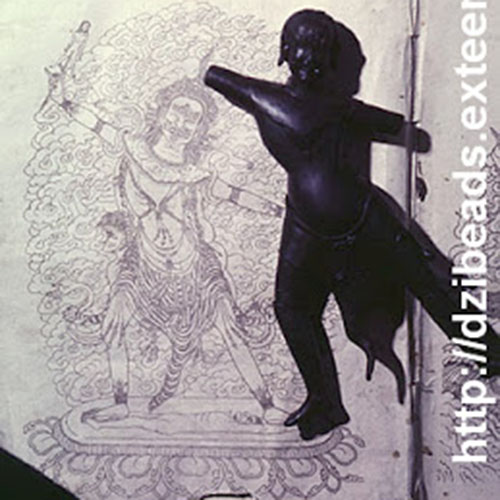 The design for Ekajata compared to the Tibetan book on which it was based.Statues Maker Are master in buddhism . | 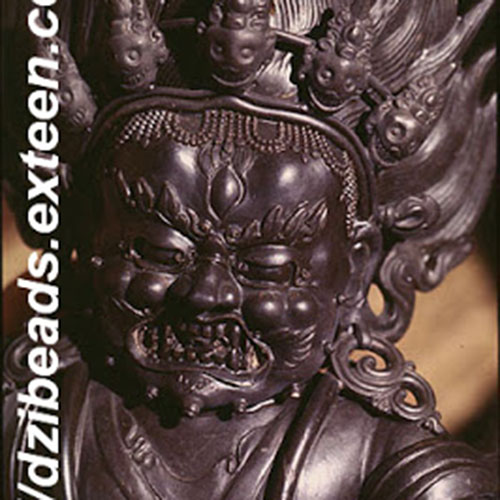 Detail of A partially finished Candamaharoshana (Acala) wax figure made in the Tibetan style. | 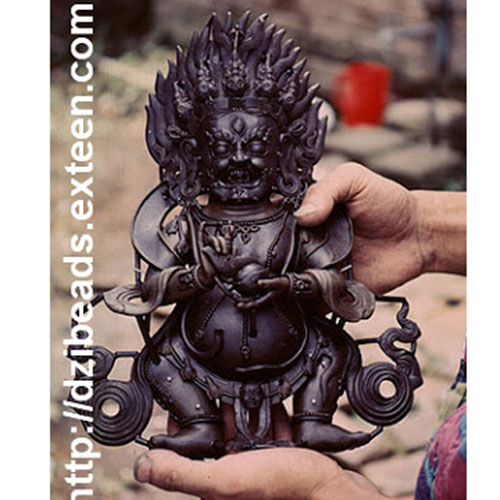 A finished wax image of Mahakala. |
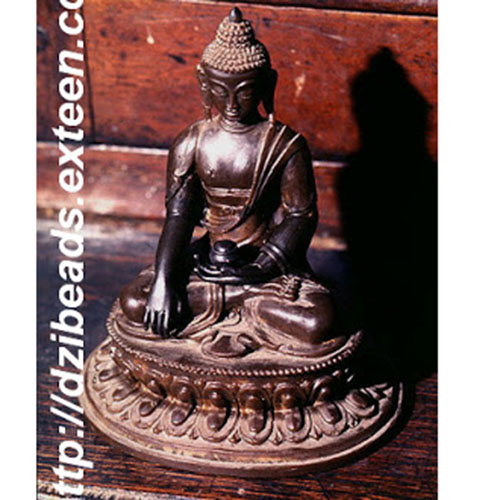 Anthor Finished Wax Model of Shakyamuni Buddha | 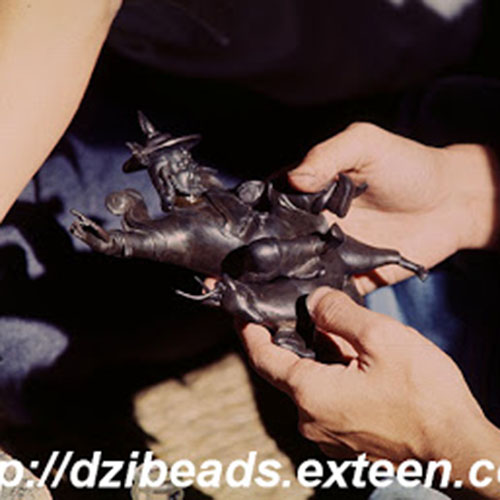 One of the modelers working in the room shows the Pehar image on which he is working. | 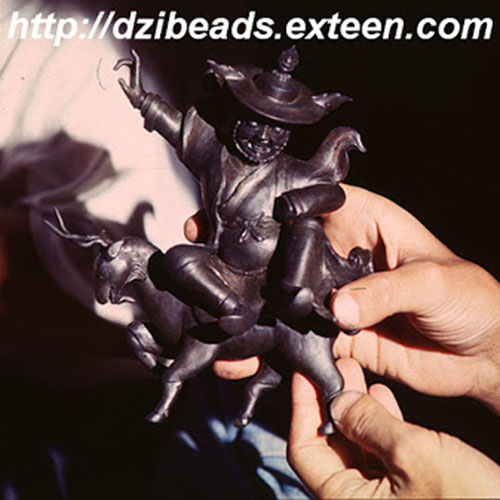 The artist showed how the goat , which had been completed earlier, fits under the image. , |
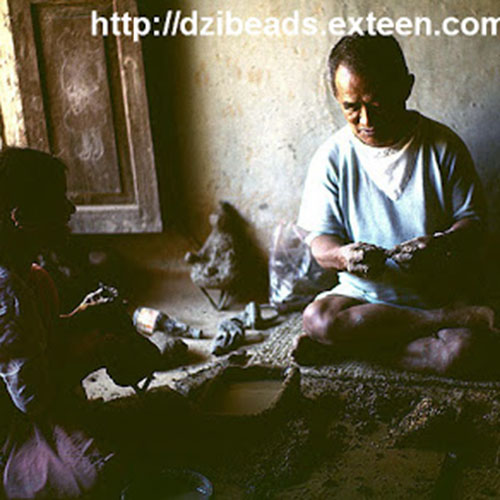 Tej Jyoti Shakya and his wife, Nani Maya Shakya Covering the wax model in a mixture of clay and dung |  Pressing the mixture of clay and dung around the wax image. | 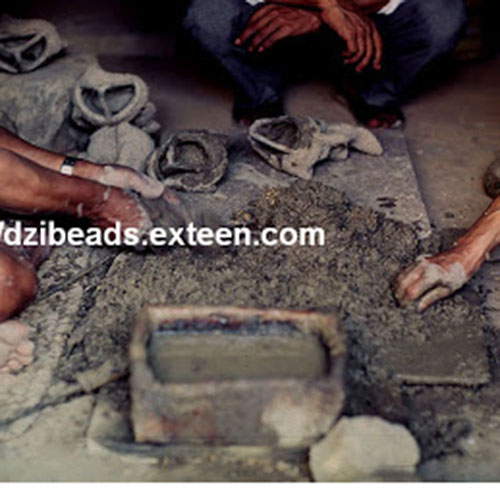 The board with the clay and dung mixture ready for use. |
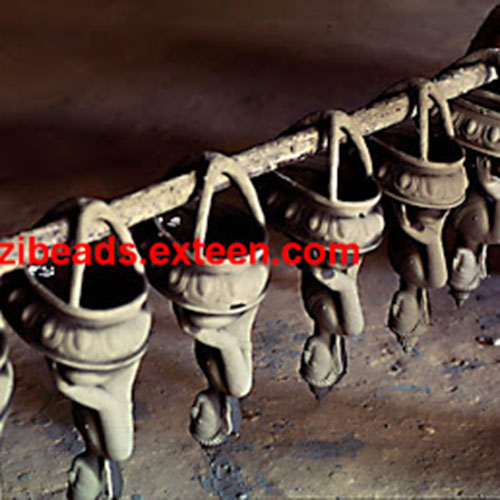
Model Pieces drying after the initial (dipped) thin layer of fine clay. | 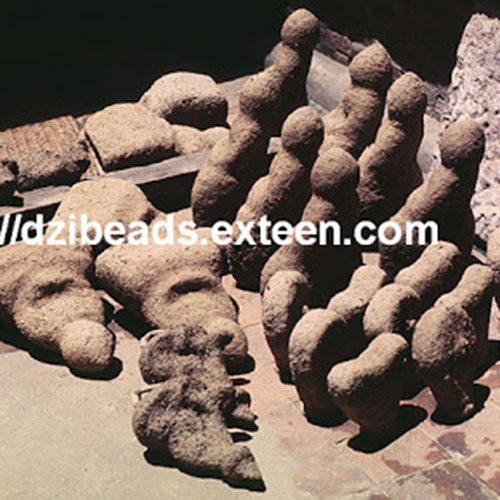
Clay-covered model pieces drying in the sun. | 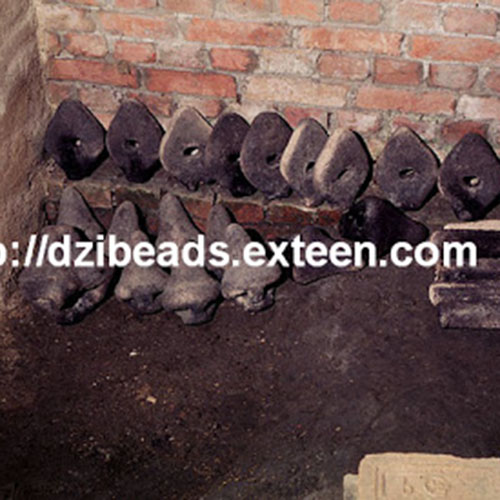
Molds waiting to be put into the burnout furnace |

The same molds, seen in the previous image, in the burnout furnace | 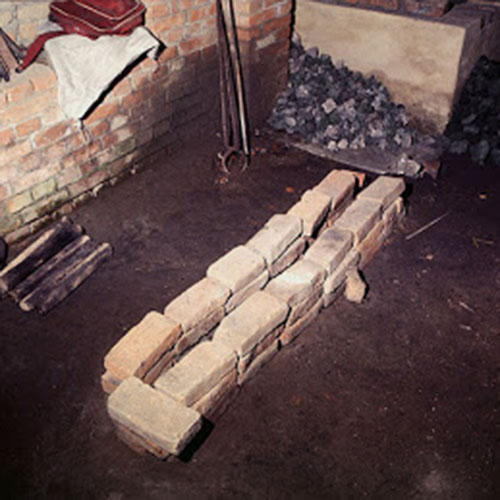
The double row of refractory bricks used to support the heated molds during casting. | 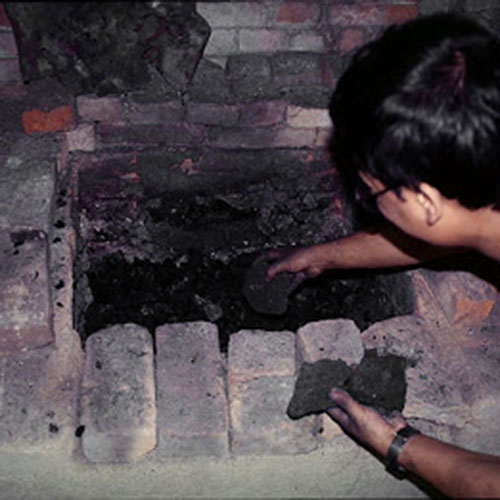
The melting furnace and a pile of coke used for melting the metals. Laying the bed of coke in the melting furnace. |
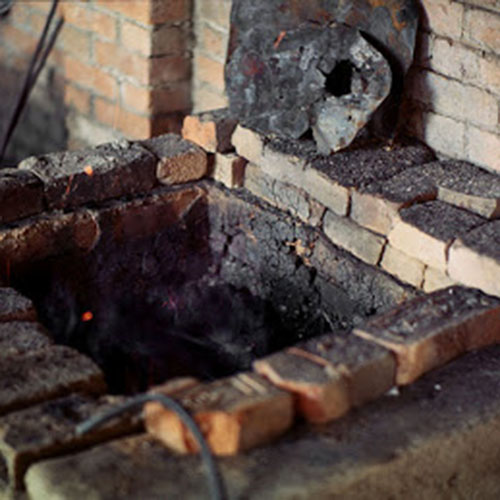
The first ignition of the coke. | 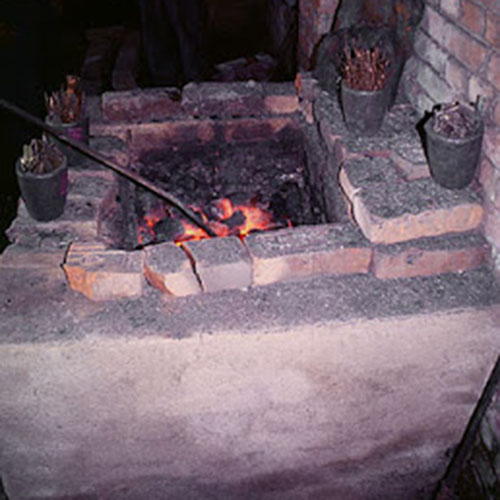
Checking the coke bed. | 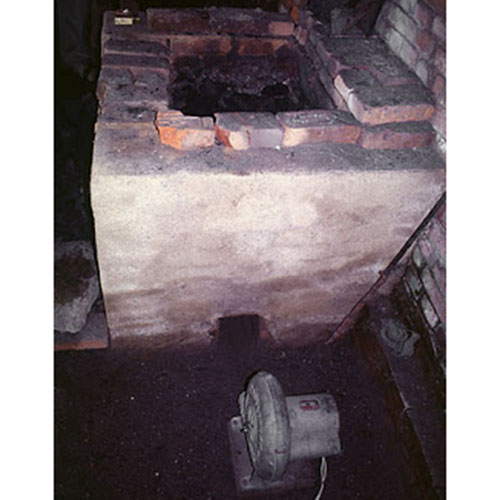
The electric blower used to force air into the melting furnace |
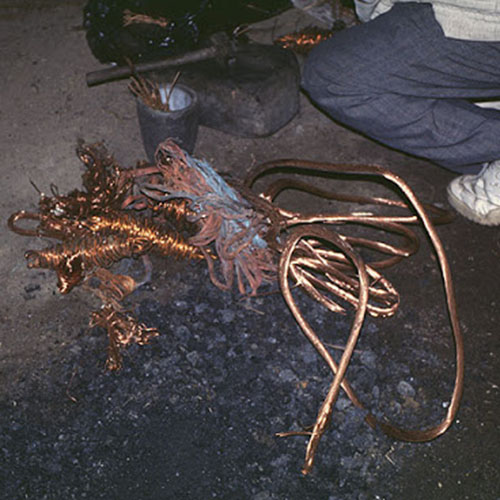
Beginning to fill the crucibles with scrap copper. | 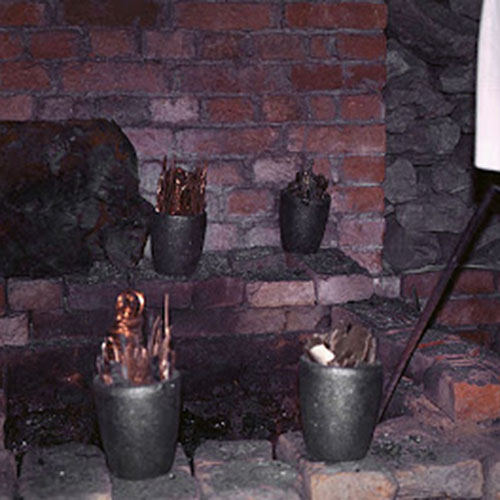
Preparing the bed of burning coke to receive the crucibles | 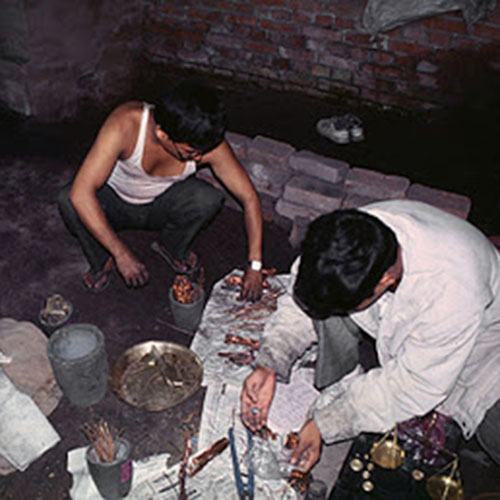
Sorting various metals used in the alloys. |
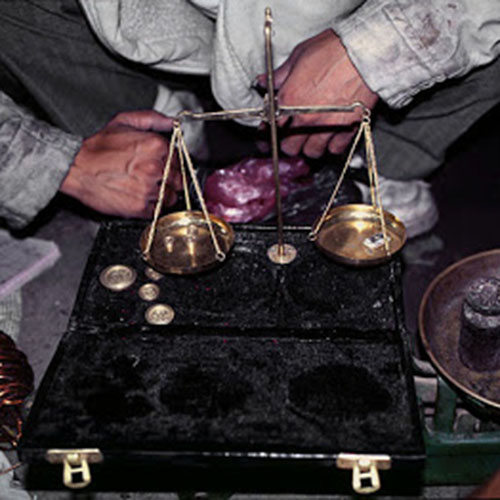
Weighing precious metals that are used in the alloys | 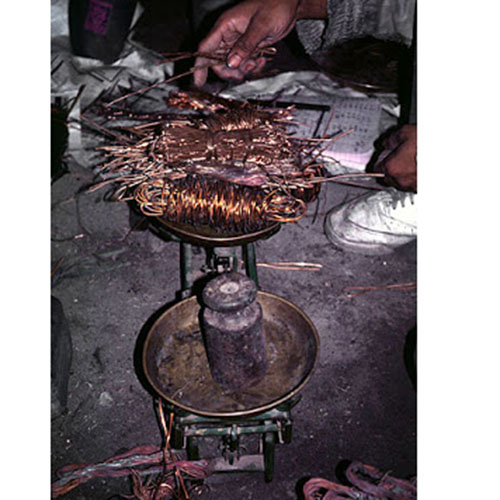
Weighing copper from Singapore to achieve a correct alloy. | 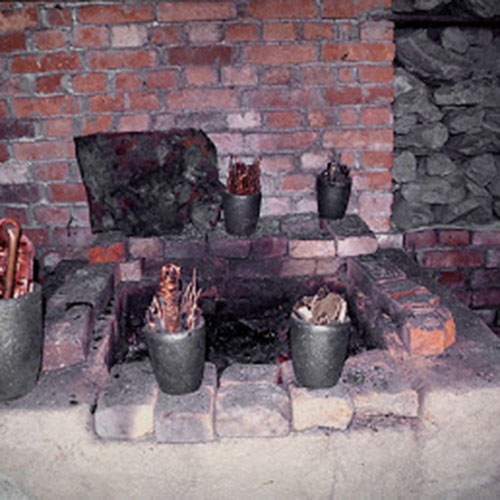
Different sizes of crucibles and various types of metals to be cast in this melt. |
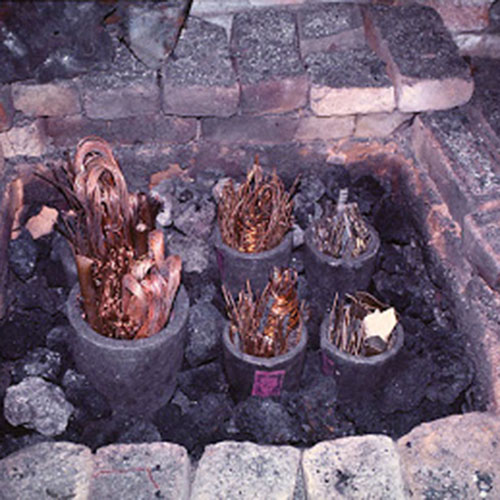
Placing the crucibles in the bed of coke filled with metal are in place. | 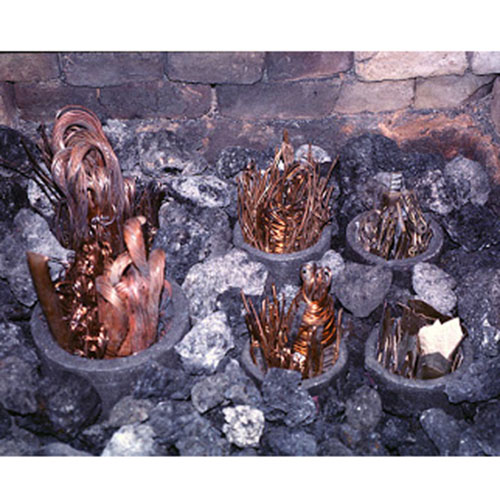
After the crucibles are in place, more coke is piled around them. | 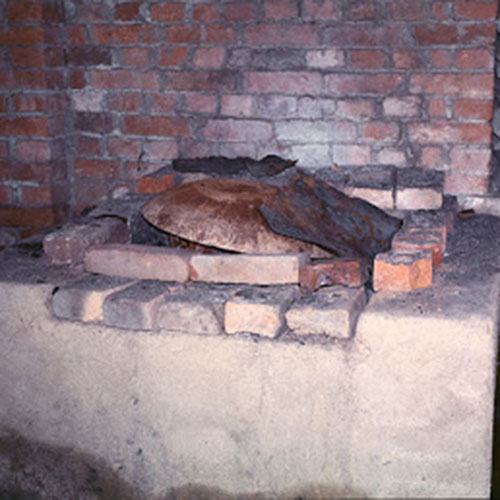
The crucibles are covered with scrap metal to hold in the heat. |
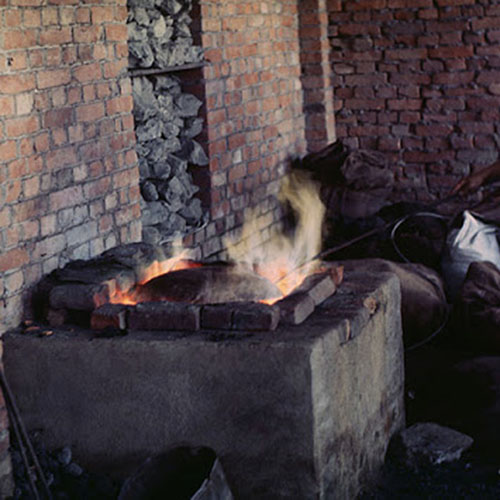
The electric fan is then connected.Soon a very hot flame is produced. | 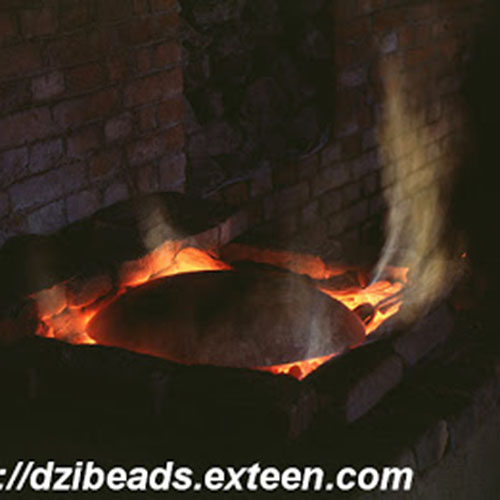
The entire furnace temperature goes up to about 1800 -1900 degrees. | 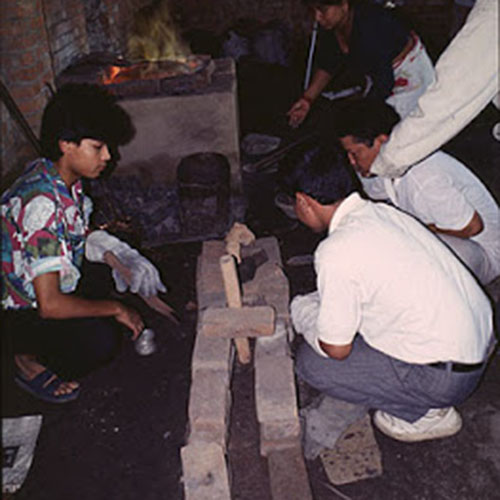
Setting up molds in between the refractory bricks to receive the molten metal. Handling the molds with asbestos gloves and bracing them with fragments of bricks. |
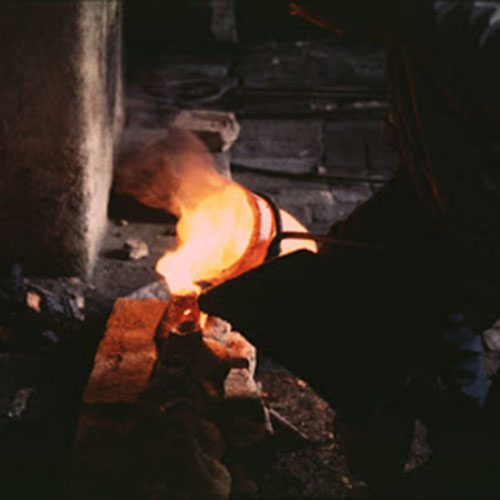
Pouring the molten metal into the base of a mold | 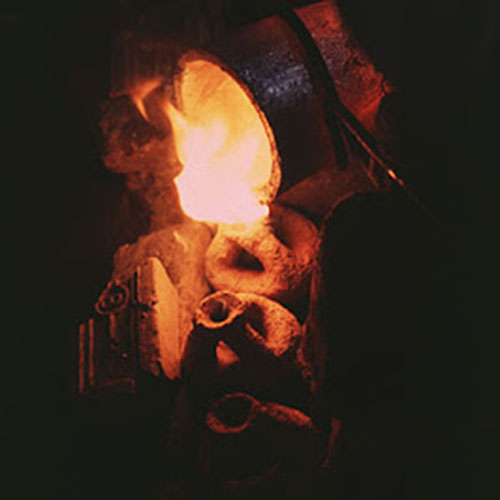
Another view of the artists pouring the molten metal.Detailed view showing the molten metal being poured into the sprues. | 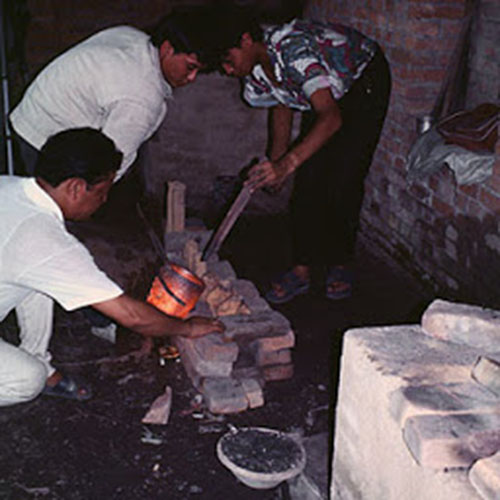
Preparing to lift and pour molten metal from one of the larger crucibles. |
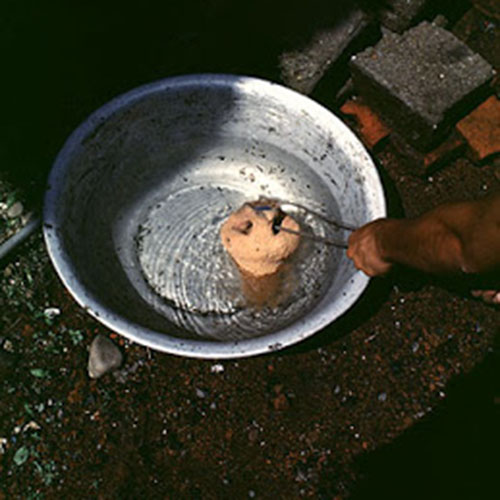
Cooling a mold containing the recently poured metal.
| 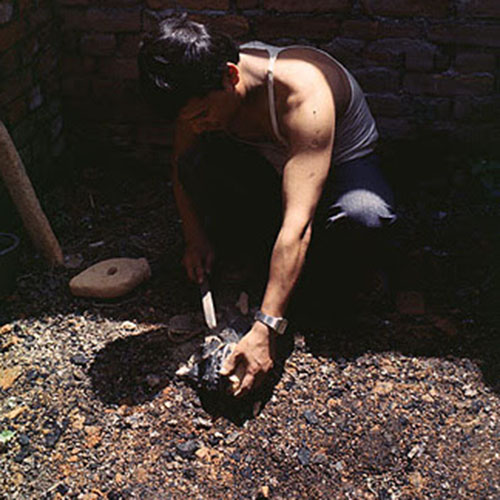
Beginning to break away the clay mold from the metal casting. The mold breaks away revealing the metal image inside | 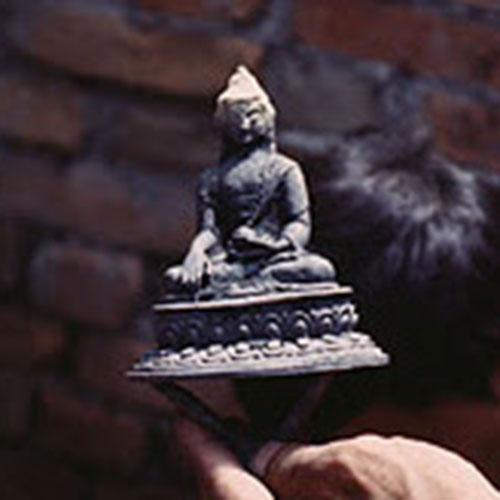
The first metal image from the day's work. |
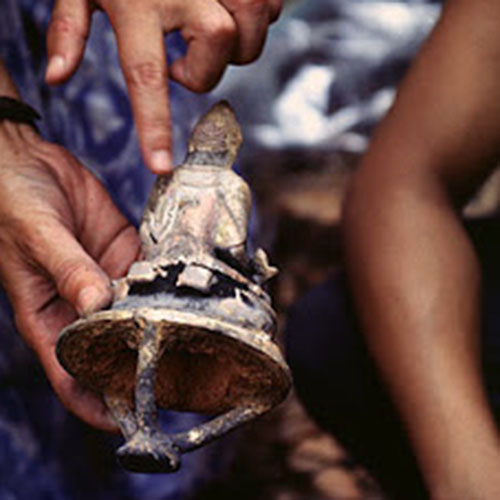
Examining the image for flaws | 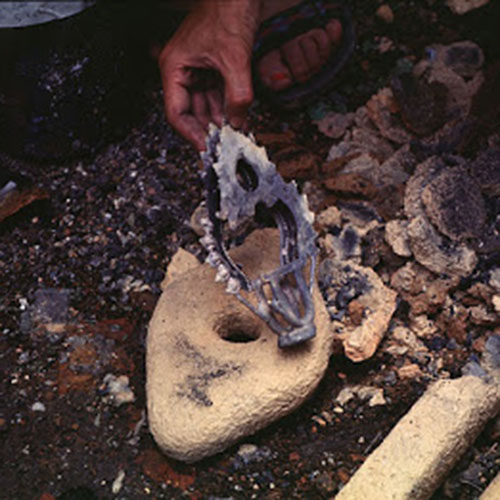
Two auras (prabhamandalas), one that cast perfectly and one (in front) that only partially filled. | 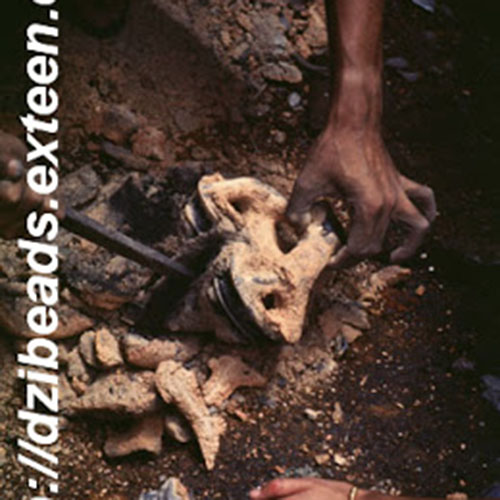
Opening more molds |
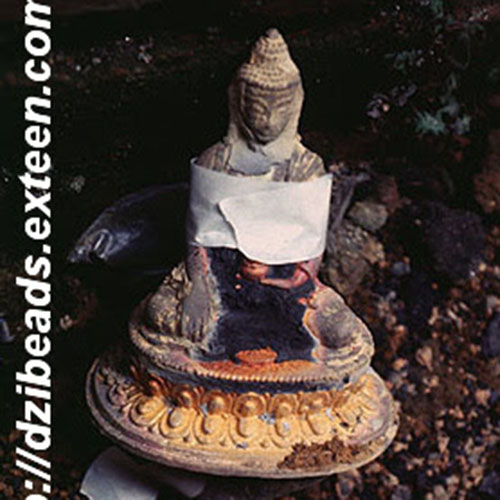
| 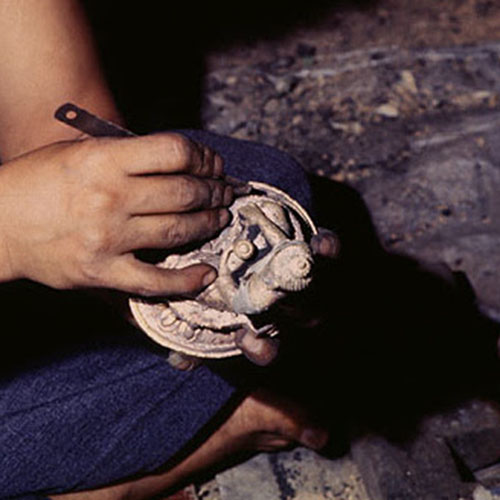
| 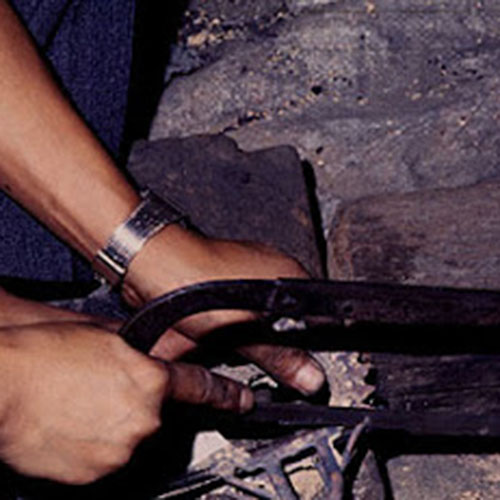
|
Researchers mark specific metal images for future identification. | Cleaning the details of the image with a metal tool. | Sawing off the sprues from Aura image. The sprue metal will be reused in future castings. |
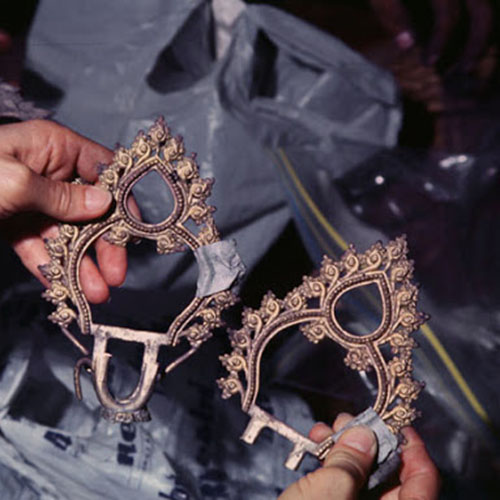
| 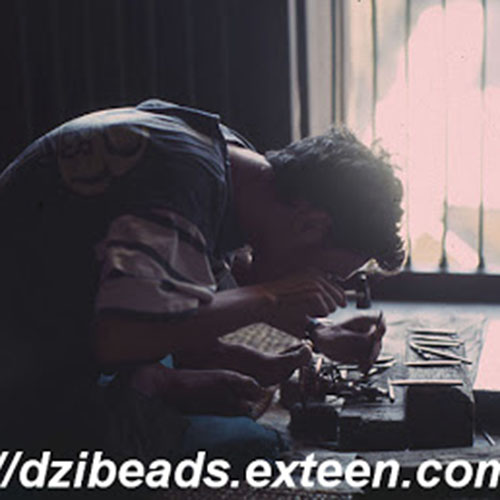
| 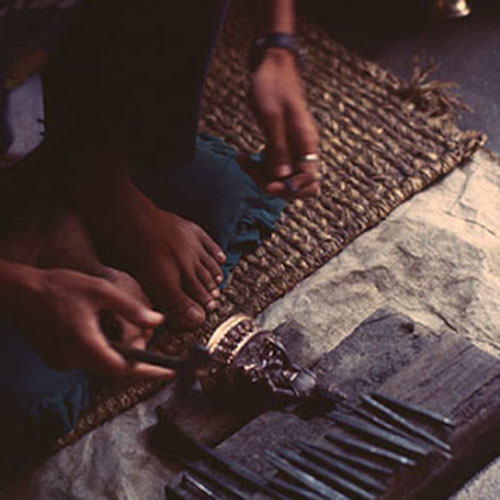
|
Two auras that worked perfectly. The one on the right has been cut off of the sprues, while the one on the left still has the sprues attached. | The finishing specialist begins the finishing process with a set of tools, including a small hammer. to give more detail | The entire surface of the image will be gently hammered to a final, almost polished finish. |
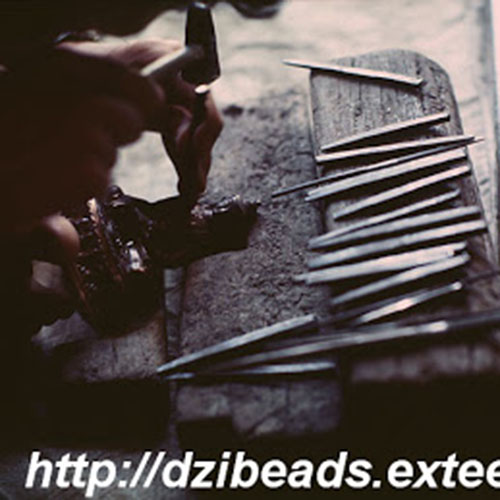
| 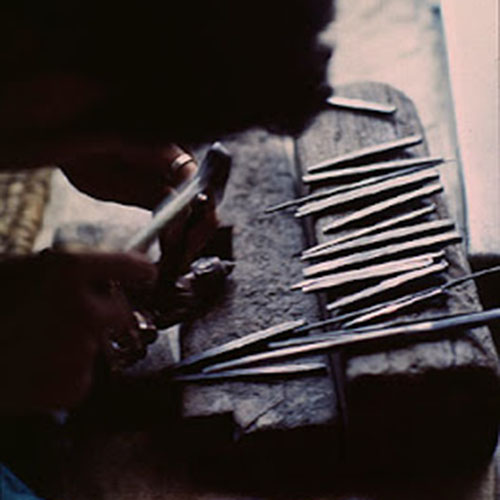
| 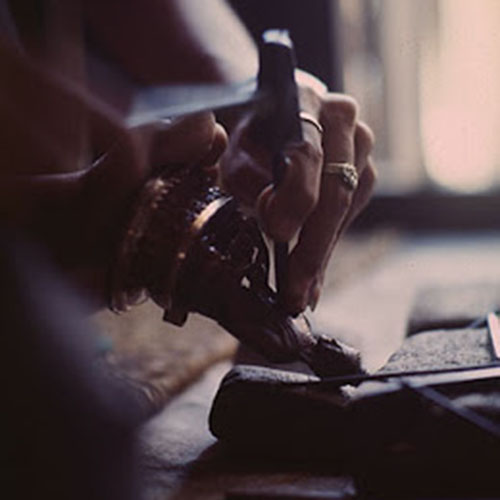
|
The finisher's tools and the work in progress | Finishing work on an image of the Buddha. | Hammering the chest of an image that is being held against the work block |
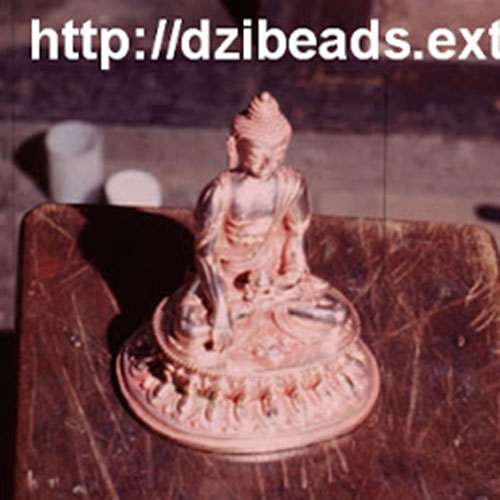
| 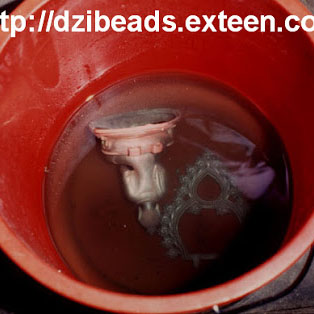
| 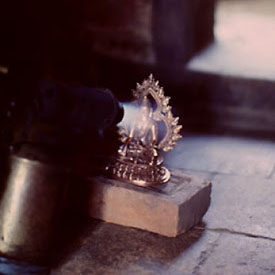
|
A Buddha image hammered and chased to the final, detailed finish. | Cleaning in a very mild acid bath. The image and prabhamandala are placed in a final acidic bath to make sure the surface is absolutely clean. | Drying the image with a blow torch. |
Read More